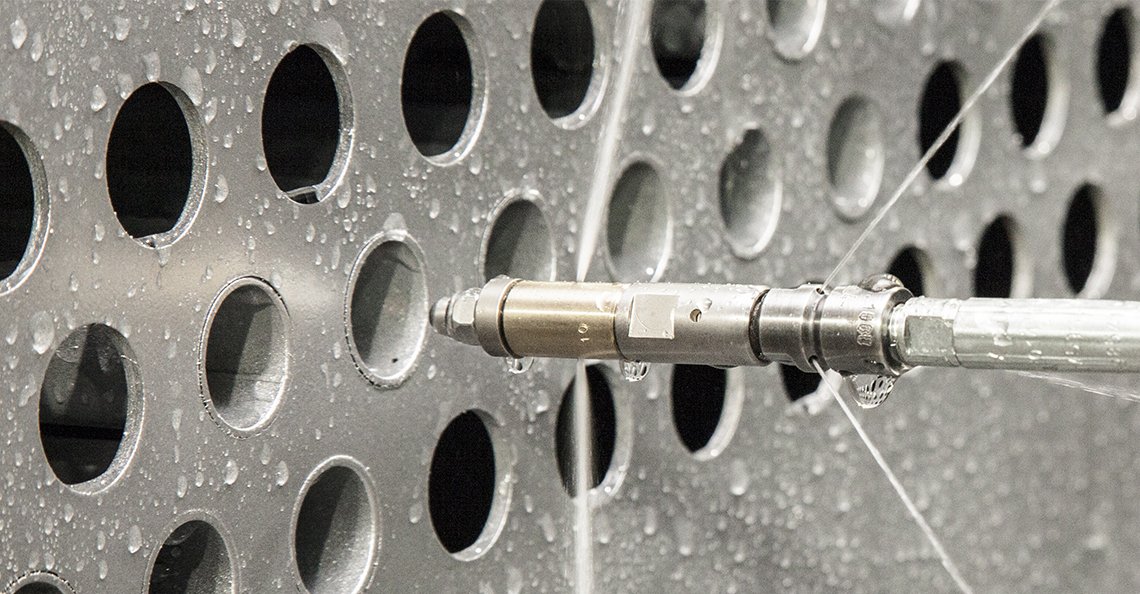
- Jul 13, 2020
- Jamie
- Heat Exchange, Servicing
- 0 Comments
Like all mechanical equipment, heat exchangers require a regimen of regular maintenance. As fouling and corrosion are two of the most common causes of performance degradation, heat exchanger cleaning is one of the most common, and most important maintenance tasks for your heat exchangers. In fact, cleaning is one of the most frequent maintenance jobs carried out at our branches and on our customer sites.
There are three main types of heat exchanger cleaning, each of which have their own advantages and disadvantages, depending on your process and plant setup:
- Chemical Cleaning, which often involves flushing with fluids to remove or dissolve dirt
- Mechanical Cleaning , which involves physical removal of dirt from tube services
- Combination Cleaning, such as Vibrasonic, which involves aspects of both
Chemical Cleaning
One big advantage of chemical cleaning is that you often do not need to dismantle the unit from the process, provided it is taken offline and cleaning connections are provided. The unit is usually isolated to contain the cleaning fluid. The disadvantages are that the cleaning fluids are often harmful and disposal is often a problem. Also some chemicals, if not monitored correctly, can actually initiate corrosion.
The physical method of adding the cleaning chemicals varies according to
- Elevated or ambient temperature
- Type of filling of fluid ie. Fill and Soak, Fill and Agitate or Fill and Circulate
- Use of liquid chemical, vapor chemical, foam chemical or emulsion.
Circulating cleaning fluid will tend to improve foulant removal rate.
A high rate of circulation may be difficult to achieve if cleaning connections are small or if the heat exchanger is blocked. Air sparging can be used to create agitation without circulation.
Chemical cleaning is often done in stages to achieve a complete clean. The best type or combination of fluids or gases to use are determined by the above points, as well as lab tests against specific fouling deposits. The end result will be a recommendation to use acids, alkalis, oxidants or solvents.
A huge choice of cleaning acids are available. For example: hydrochloric, nitric, sulphuric, and more. Often inhibitors are added to stop the acid attacking the surface of the heat exchanger itself.
Cleaning alkalis such as caustic soda, and ammonia are often used for removal of organic foulants such as fats and greases.
Oxidants such as potassium permanganate, sodium bromate, and sodium nitrite form a stable oxide layer on the cleaned surface which creates a shell against corrosion. This particular method of cleaning is known as passivation.
Solvents including aromatic hydrocarbons, aliphatic hydrocarbons and chlorinated hydrocarbons are used to dissolve specific deposits but are heavily regulated.
Other agents can be added to assist with the cleaning process such as Biocides, Surfactants, Inhibitors, Antifoams and Dispersants. A thorough design process will have taken your process into account and will include cleaning recommendations. And your heat exchanger service experts should be able to advise you on the best combination of chemicals and additives to achieve the results you need.
Mechanical Cleaning
Mechanical cleaning is another way to maintain heat exchanger performance, however it requires access considerations and often requires the unit to be removed from the process entirely, so the servicing team can access all parts of the bundles.
In our teams’ experience, we often find that access to inside of tubes is usually easy on Shell and Tube type exchangers but U tubes can present some challenges. If the original designer has taken cleaning and maintenance into account, they may have included removable bundles, square, or large pitches to make access easier.
As for the cleaning equipment itself, there are nearly as many types of tools as there are exchangers to be cleaned. To remove soft deposits, servicing teams will use a combination of brushes, scrapers, and drills (manual or motor driven, with or without water flushing). Mechanical cleaning can be used on tube side or shell side but care has to be taken that the tools are used correctly to not cause damage.
For brittle and hard deposits, high-pressure water jetting is a common mechanical cleaning process, with pressure ranges of 200 to 3000 Bar. The water enters cracks on the fouling, forcing the crack to propagate and fracturing the deposit, allowing it to be flushed away. Hydro Jetting is also a very efficient method of mechanical cleaning, and is often used on a large number of exchangers at once, for example during a refinery turnaround.
Vibrasonic Cleaning
There are also combination cleaning methods of the two aforementioned types – using mechanical methods to enhance the effectiveness of a cleansing chemical mix. Serck’s vibrasonic cleaning service is an example of this. Vibrasonic cleaning uses pneumatically driven turbines to produce sinusoidal wave patterns through a uniquely formulated cleaning fluid, leveraging the benefits of both mechanical agitation and chemical dissolution to achieve a deep, thorough and rapid cleaning, while being highly cost-effective. Serck are proud to own one of the UK’s largest Vibrasonic tanks at 3m x 1.5m x 1.5m.
How often should my heat exchanger be cleaned?
So how often should you clean your heat exchangers? Frequent cleaning is proven to save energy and unplanned downtime, however this must be balanced with any productivity lost from even the most carefully scheduled shutdowns.
Historical data from thorough maintenance records can help site maintenance engineers build up an efficient cleaning schedule. We are also seeing Industrial Internet of Things technology (IIoT) advances in this area, where condition-based monitoring can alert to reduced performance before emergency maintenance is needed, and without over-scheduling process-limiting maintenance before it’s truly needed. This will also self-optimize your cleaning frequency to your particular fluids and equipment.
For advice or further information about this technology, a chat on which cleaning process might serve your site best, or any other heat transfer needs, contact us today.
Recent Comments