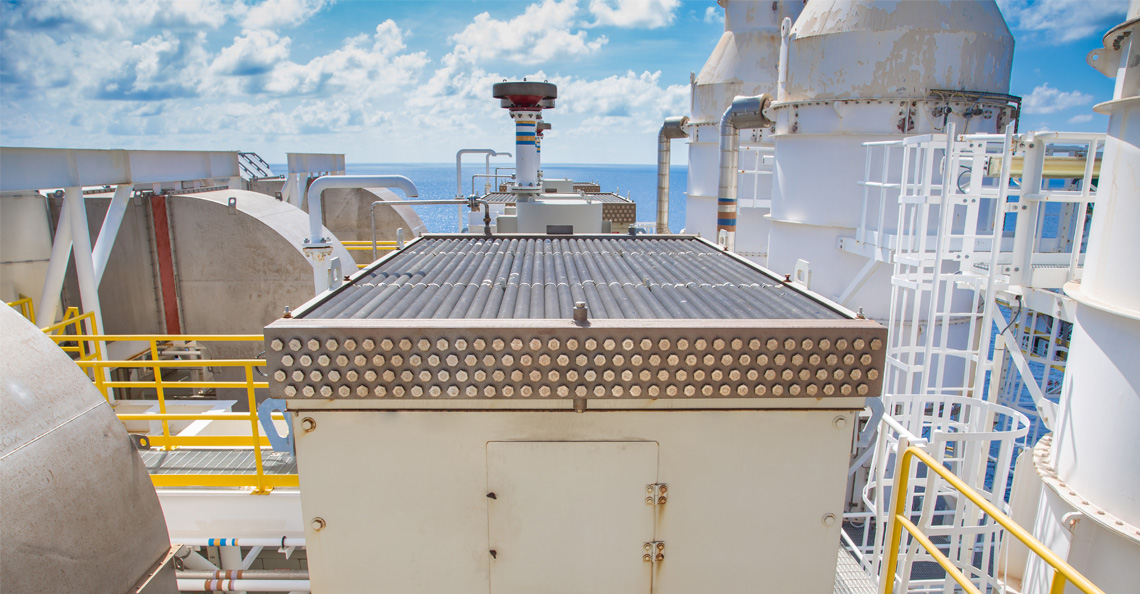
- Oct 12, 2021
- Atul
- Heat Exchange, Oil Cooler, Production, Servicing
- 0 Comments
Why Oil Coolers?
Hydraulic and lubrication oil systems are used in many industrial, mobile, and aerospace applications to reduce machine wear and increase performance. Some examples include turbine generators, hydraulic machines and heavy-duty engines. High pressure pumping and friction in the moving parts of all these applications add to the heat in the oil.
This is where oil coolers come into play: they remove this excess heat. Proper hydraulic and lubricant oil temperature control is very important for critical and high value machines to maintain high efficiency and avoid catastrophic break downs.
At higher temperatures hydraulic & lubricant oil loses its viscosity. When this happens, the oil film becomes thinner, resulting in accelerated wear and tear and even scuffing conditions. This can lead to a catastrophic failure without warning. Higher temperatures also cause the oil to age sooner, the additives to deplete quicker, and accelerates the formation of sludge resulting in corrosion. It can also lead to internal oil leakage.
In fact, a commonly accepted rule states that hydraulic oils & lubricants will degrade twice as fast for every 10 degrees Celsius rise in temperature beyond their base activation temperature. Keeping your oil cool extends its life, and the life of your equipment. Inversely, if one were to reduce the oil temperature by 10 degrees Celsius, one would then expect to double the life of the oil.
Which Oil Cooler Should I Choose?
There are a number of oil cooler construction types, and the one best for your application will take into consideration your space constraints, process fluids, pressure and volume. Broadly, some of the solutions are:
Plate Heat Exchangers (PHE)
These can be used to cool oil and provide high cooling efficiency. There are two types of PHE: brazed or gasket. Brazed PHEs, where the plates have been sealed via a brazing material between the plates, can operate at much higher pressure but are difficult to clean and service. Gasket type coolers can be opened for servicing and cleaning, and can have the individual gaskets & plates easily replaced and reassembled.
Both types of plate heat exchangers can be built using various materials including titanium or stainless steel for highly corrosive cooling media applications.
Shell and Tube Oil Coolers
Shell and tube style oil coolers can be used for higher flow rates using chilled water or glycol solution as cooling media. Their design means these can be very easy to clean. They can also handle higher contamination in oil compared to plate heat exchangers. Enhanced low fin tubes could be used to increase thermal efficiency.
Air Blast Oil Coolers
Using forced draft ambient air, oil is cooled in a finned tube cooling matrix and returned back to the system. These can also handle high operating pressures and large volumes of oil.
Plate and Bar Coolers
These are full aluminum compact heat exchangers, and are very efficient. They also use forced draft ambient air for cooling. You could use Serck’s plate and bar cooler selection sheet to quickly size your cooler.
Oil Chillers
In case of extreme heat input conditions oil chillers can also be used.
Serck designs and manufactures oil coolers of various construction types. Based on your data of oil flow, oil viscosity and load we can design and manufacture an oil cooler specifically designed and built for your application. These can enhance the life of your critical equipment and save you money with longer uptime for your machines. For more information, contact us today.
Recent Comments