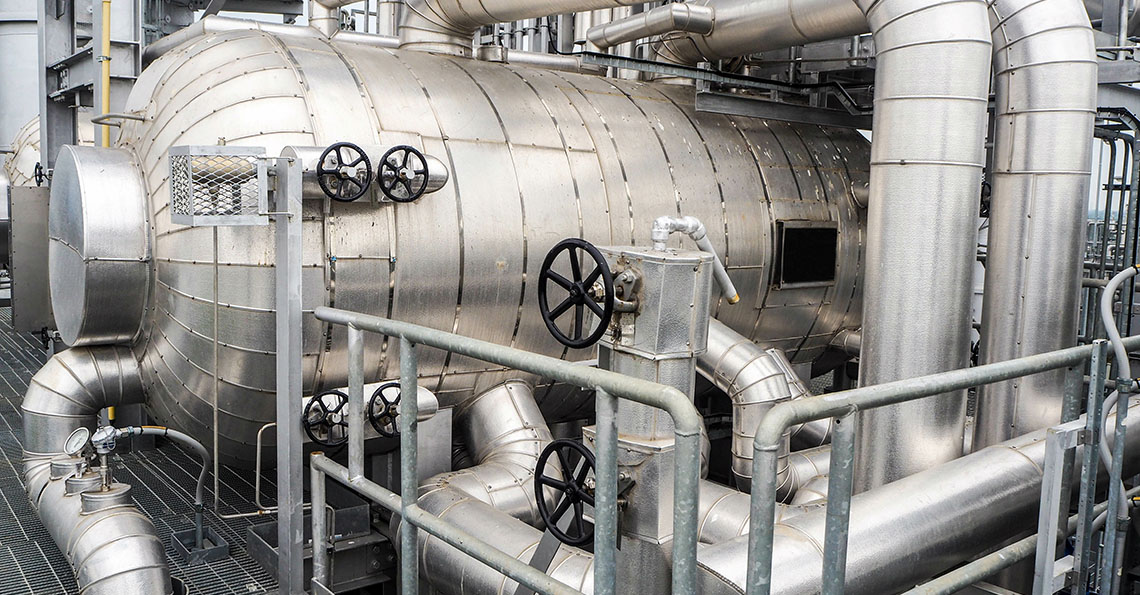
- Dec 8, 2021
- Atul
- Heat Exchange, Industry, Servicing
- 0 Comments
Avoiding Boiler and Heat Recovery Steam Generator (HRSG) Tube Failures
One of the main reasons for Boiler and Heat Recovery Steam Generator (HRSG) tube failures is scaling, which occurs as minerals and oxides from the feedwater precipitate and adhere to tube surfaces.
Scaling can lead to failure in two ways:
- Overall reduction in the effectiveness of heat transfer, thus causing tubes to overheat, and;
- Corrosion, due to build-up in tubes, leading to tube failures.
In both cases, to minimize scaling, proper feed water purification and chemical treatment is required.
Corrosion can occur even in clean boiler tubes but the likelihood of corrosion is much higher in porous scaling deposits. Corrosive contamination concentrates are formed in the scale pores and can be much higher in concentrated form than in the boiler water, thus accelerating corrosion. Because of this, as deposits accumulate, the control of water chemistry becomes increasingly important.
Avoiding Boiler and Heat Recovery Steam Generator (HRSG) tube failures via Identification of Corrosive Agents
To avoid Boiler and Heat Recovery Steam Generator (HRSG) tube failures, identification of corrosive agents is key. Corrosion is often caused by concentrations of chemicals such as sodium hydroxide, sodium carbonate, magnesium chloride, and magnesium sulfate. Dissolved carbon dioxide and oxygen can also cause corrosion and must be removed from the feedwater.
Ultimately, identification of the root cause of corrosion is the only way to avoid repeated failures. Chemical analysis of the deposits can suggest the cause. Deposits may contain caustic agents or acids.
- Magnesium hydroxide in deposits suggests the presence of acid-forming precipitation. Sodium ferrate indicates caustic condition.
- Organic deposits suggest corrosion by organic compounds and excessive ferric oxide or hydrogen dioxide with pitting suggest oxygen attack. Common observations are oxygen pitting, caustic corrosion, organic corrosion and phosphate corrosion.
- Cross section Metallography can detect other forms of corrosion which are microscopic and below the surface. These include intergranular corrosion, stress corrosion cracking and hydrogen damage.
Overheating causes “thin lip” burst of tubes Caustic gouging of tube Hydrogen-induced cracking Oxygen pitting in economizer tube Stress corrosion cracking with a branched structure
Chemical cleaning to remove internal scaling build-up
Inspection and Cleaning of any accumulation of scale at regular intervals is an absolute must to avoid tube failures.
In general, the chemical cleaning follows these steps:
- The tube internals are flushed with a solvent containing inhibitors to dissolve any scale
- Next the tubes are flushed with water to flush the debris.
- Then the unit is treated with a neutralizing and passivating solution
- Finally the unit is flushed again with water to remove any remaining loose deposits and chemicals
There are many Alkaline and Acidic chemicals available. The ones appropriate for your boilers or HRSG will depend on the tube material.
Additional information on managing your feed water to minimise and treat corrosion can be found at:
The Suez Handbook of Industrial Water Treatment
The Association for Materials Protection and Performance
Serck designs and manufactures various heat exchangers for boilers and heat recovery steam generator units. For any of your service, repair or replacement needs, contact us today.
Recent Comments